The growing prevalence of counterfeit components poses significant risks to industries that rely on precision and reliability. This threat impacts sectors such as aerospace, defense, and commercial electronics, where the consequences of counterfeit parts can range from reduced equipment performance to operational failures and even life-threatening situations. Maintaining supply chain integrity is essential for preventing counterfeit parts from compromising critical systems. Summit Interconnect, a leader in this field, implements robust risk mitigation strategies that position it as a trusted partner in both military and commercial sectors.
Counterfeit Parts: A Growing Threat
Counterfeit parts are infiltrating global supply chains, introducing serious risks for manufacturers and consumers alike. For example, in 2022, the delivery of 18 F-35 fighter jets was halted after a Chinese-sourced magnet in the engine was discovered, in violation of federal procurement laws. Although the magnet did not pose an immediate risk to safety, the incident underscored how counterfeit parts can disrupt military operations and violate procurement integrity. (Defense News)
The threat of counterfeit components extends beyond defense. In the broader electronics industry, counterfeit parts cause significant financial losses and system failures.
“Experts have estimated that as many as 15 percent of all spare and replacement semiconductors purchased by the Pentagon are counterfeit. Overall, we estimate that counterfeiting costs US based semiconductor companies more than $7.5 billion per year, which translates into nearly 11,000 lost American jobs.”
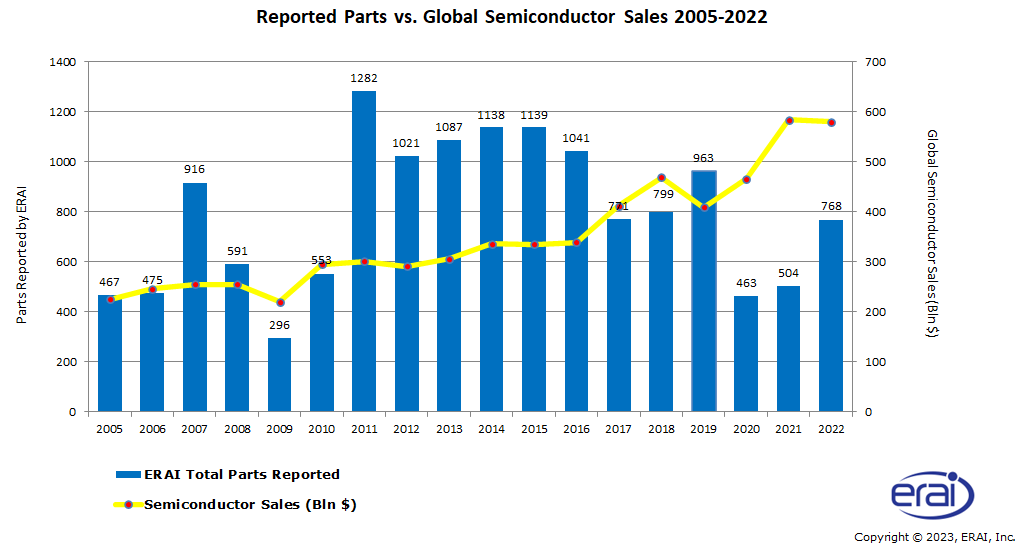
Similar trends affect commercial sectors, where counterfeit parts reduce the lifespan and reliability of products. Counterfeit components are not only difficult to detect but can also result in costly recalls and damage to a company’s reputation.
The current shortage of semiconductors and other electronic parts has exacerbated the problem, pushing companies to source components from secondary markets where the risks of counterfeit parts are significantly higher. This problem is particularly challenging in sectors that rely on long-lasting, mission-critical systems, such as defense and aerospace, where the consequences of a failure due to counterfeit parts can be catastrophic.
The Need for Risk Mitigation
In the face of these growing threats, risk mitigation strategies have become an essential element of supply chain management. Effective risk mitigation involves sourcing components exclusively from vetted, authorized suppliers, ensuring traceability throughout the supply chain, and conducting rigorous testing and quality checks.
Modern risk mitigation techniques for printed circuit boards involve using AI-driven inspection tools and advanced imaging technologies such as X-rays to identify counterfeit components early in the process. By employing these technologies, manufacturers can detect discrepancies in components before they enter production, reducing the likelihood of counterfeit parts making their way into finished products. Additionally, implementing real-time monitoring systems throughout the supply chain ensures that potential risks are flagged and addressed before they can cause significant disruptions.
Maintaining traceability is another crucial element of risk mitigation. By keeping a record of each component’s journey through the supply chain, from procurement to final delivery, companies can quickly identify and isolate issues if a counterfeit part is discovered. This level of transparency not only enhances product reliability but also strengthens trust between manufacturers and their clients, particularly in high-stakes industries like defense and aerospace.
Summit Interconnect’s Commitment to Supply Chain Integrity
Summit Interconnect stands out in the industry for its proactive approach to preventing counterfeit parts from entering its supply chain. Through a rigorous vendor approval process, Summit ensures that all suppliers are thoroughly vetted and must meet strict standards for authenticity and reliability. Unlike many competitors, Summit enforces a zero-tolerance policy toward unauthorized suppliers, reducing the risk of counterfeit parts from the outset.
Summit Interconnect employs a comprehensive, multi-step approval process to ensure the authenticity and quality of all components, protecting against counterfeit risks. All suppliers must comply with the PUC-P-0003 Supplier Quality Requirements, which dictate strict guidelines for parts traceability and sourcing.
- Parts Traceability: For orders requiring traceability, suppliers must provide full certification upon request from the customer.
- Corrective Action: If a supplier fails to meet traceability requirements, the Purchasing Manager initiates corrective action, and non-compliant suppliers may be removed from the Approved Supplier List (ASL).
This rigorous process ensures that only high-quality, verified components enter Summit’s supply chain, maintaining supply chain integrity and minimizing risks associated with counterfeit parts.
At the core of Summit’s strategy is its focus on traceability. Every component used in production is tracked from the moment it is sourced to its final integration into the product. This high level of traceability allows Summit to maintain complete control over its supply chain, ensuring that each part meets the required standards for quality and reliability. In the event that a counterfeit component is suspected, Summit’s traceability protocols enable rapid identification and isolation, preventing further contamination of the production line.
To avoid using counterfeit parts, electronic design engineers can take several proactive steps. First, use a trusted manufacturer. Select well-known, reputable manufacturers with experience and proven track records in the industry. Verify that the manufacturer regularly evaluates and audits suppliers to ensure they adhere to quality standards and have robust anti-counterfeiting measures in place. Second, allow your PCB manufacturing partner to procure components using its authorized and vetted suppliers. Third, stay informed about counterfeiting trends with industry news and reports regarding emerging threats. And finally, provide a Bill-of-Materials (BOM) that is accurate with components that have relevant certifications (e.g., AS5553 for counterfeit avoidance) and comply with industry standards. This will also help avoid substitutions that might introduce counterfeit components.
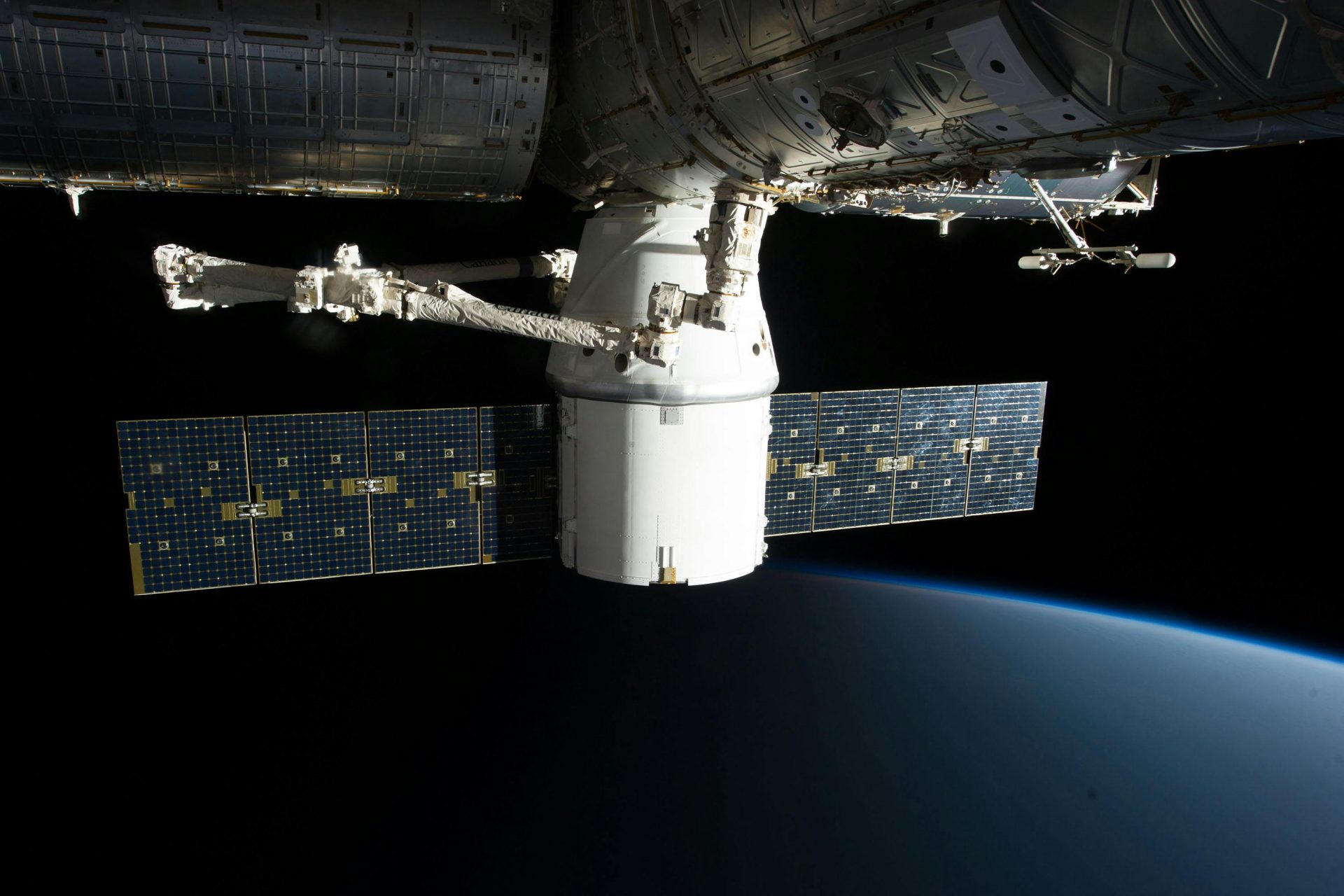
Trusted by Both Military and Commercial Clients
The military sector is particularly vulnerable to counterfeit parts, as failures in mission-critical equipment can result in loss of life and compromise national security. For this reason, defense clients demand the highest standards of authenticity and reliability from their suppliers. Summit’s commitment to supply chain integrity and risk mitigation has made it a trusted partner in the defense industry, where ensuring the authenticity of components is non-negotiable.
Summit’s proactive approach to counterfeit prevention is also highly valued in the commercial sector, where counterfeit components can lead to costly recalls, reduced product performance, and reputational damage. Summit’s counterfeit prevention policies and processes offer commercial clients the peace of mind that their products will meet the highest standards for reliability and performance, even in times of global supply chain disruption.
Case Studies: Proven Track Record
The incident involving the F-35 fighter jets serves as a cautionary tale for the defense industry, illustrating how even a single counterfeit component can disrupt an entire project. Summit’s robust vendor approval and real-time monitoring processes are specifically designed to prevent such issues from arising. By detecting potential risks early, Summit is able to maintain smooth operations and ensure that projects remain on schedule.
In the commercial sector, Summit has demonstrated its leadership by collaborating with industry partners to implement an Anti-Counterfeit Policy that ensures compliance with traceability requirements and reduces the risk of counterfeit parts entering the production process. Summit’s commitment to transparency and accountability sets it apart from competitors and reinforces its position as a leader in supply chain integrity.
What can Engineers Do?
Engineers play a crucial role in minimizing the risk of counterfeit parts infiltrating supply chains. By adopting certain best practices, engineers can help safeguard against these threats.
- Design with Security in Mind: Engineers should design products that include tamper-resistant or tamper-evident features, such as unique identifiers or embedded technologies that make counterfeit replication more difficult. For instance, incorporating encrypted digital signatures on components can help verify their authenticity.
- Source Components from Trusted Suppliers: Engineers should work closely with procurement teams to ensure that components are sourced from trusted, certified suppliers with strong track records of quality assurance and compliance.
- Implement Rigorous Testing Protocols: Engineers can establish and oversee stringent testing protocols, including X-ray inspection, functional testing, and quality assurance measures, to catch counterfeit components before they are used in production.
- Use Smart Design Features: Engineers can incorporate smart design features that make it harder for counterfeit parts to integrate seamlessly into the system. This can include using custom-designed components with proprietary features that are difficult for counterfeiters to replicate.
- Engage in Regular Supplier Audits: Engineers can participate in or initiate regular audits of suppliers to ensure they are complying with quality standards and traceability requirements. This reduces the risk of counterfeit parts entering the supply chain undetected.
By incorporating these best practices, engineers can play a pivotal role in reducing the risk of counterfeit components entering critical systems and ensuring the reliability and safety of the final products.
Counterfeit parts are a growing concern for industries that depend on reliability, precision, and safety. As these threats continue to escalate, companies must adopt comprehensive strategies for supply chain integrity and risk mitigation to protect their operations and maintain client trust. Summit Interconnect has distinguished itself as a leader in counterfeit part mitigation through its rigorous vendor approval processes, advanced detection technologies, and unwavering commitment to traceability.
Sources
Fake parts: A Pentagon supply chain problem hiding in plain sight
Battling Counterfeit Electronics in Manufacturing
Counterfeit Electronic Components: How to Identify and Avoid Them
How Counterfeit Parts Affect the Printed Circuit Boards in Your Electronic Manufacturing
THE ELECTRONICS INDUSTRY’S COUNTERFEIT PARTS PROBLEM